What is Porosity in Welding: Common Resources and Efficient Remedies
What is Porosity in Welding: Common Resources and Efficient Remedies
Blog Article
The Science Behind Porosity: A Comprehensive Overview for Welders and Fabricators
Comprehending the intricate devices behind porosity in welding is important for welders and makers making every effort for impressive workmanship. From the composition of the base materials to the details of the welding process itself, a wide range of variables conspire to either worsen or alleviate the existence of porosity.
Comprehending Porosity in Welding
FIRST SENTENCE:
Examination of porosity in welding reveals critical understandings into the integrity and quality of the weld joint. Porosity, characterized by the existence of tooth cavities or voids within the weld steel, is a common worry in welding procedures. These spaces, otherwise effectively addressed, can jeopardize the architectural integrity and mechanical residential or commercial properties of the weld, leading to potential failures in the finished item.

To spot and measure porosity, non-destructive testing approaches such as ultrasonic testing or X-ray assessment are often employed. These strategies permit for the recognition of internal problems without compromising the integrity of the weld. By analyzing the size, shape, and circulation of porosity within a weld, welders can make informed decisions to boost their welding procedures and accomplish sounder weld joints.
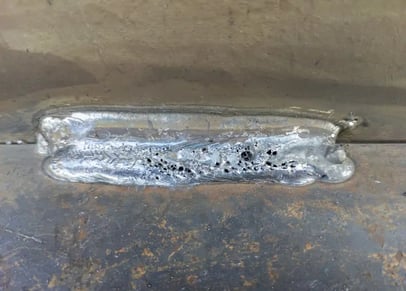
Factors Influencing Porosity Formation
The incident of porosity in welding is affected by a myriad of variables, ranging from gas shielding efficiency to the intricacies of welding criterion setups. Welding specifications, including voltage, present, take a trip rate, and electrode type, additionally influence porosity development. The welding technique employed, such as gas metal arc welding (GMAW) or secured metal arc welding (SMAW), can influence porosity development due to variations in warm circulation and gas coverage - What is Porosity.
Impacts of Porosity on Weld Quality
The presence of porosity also damages the weld's resistance to deterioration, as the caught air or gases within the spaces can respond with the surrounding environment, leading to degradation over time. Furthermore, porosity can impede the weld's capability to hold up against stress or effect, additional threatening the general top quality and integrity of the bonded structure. In essential applications such as aerospace, automobile, or architectural building and constructions, where safety and sturdiness are extremely important, the damaging effects of porosity on weld high quality can have serious repercussions, emphasizing the importance of lessening porosity through proper welding methods and treatments.
Strategies to Reduce Porosity
To boost the quality of bonded joints and ensure structural stability, welders and fabricators employ details techniques focused on minimizing the development of voids and tooth cavities within the product throughout the welding process. One efficient method to decrease porosity is to make sure appropriate material prep work. This click here for more info includes complete cleaning of the base steel to eliminate any kind of pollutants such as oil, grease, or wetness that can add to porosity development. Furthermore, making use of the proper welding specifications, such as the appropriate voltage, current, and take a trip speed, is vital in stopping porosity. Maintaining a consistent arc length and angle throughout welding additionally helps lower the likelihood of porosity.

Utilizing the suitable welding method, such as back-stepping or using a weaving movement, can additionally assist distribute warmth uniformly and decrease the chances of porosity formation. By carrying out these methods, welders can successfully lessen porosity and generate high-grade welded joints.
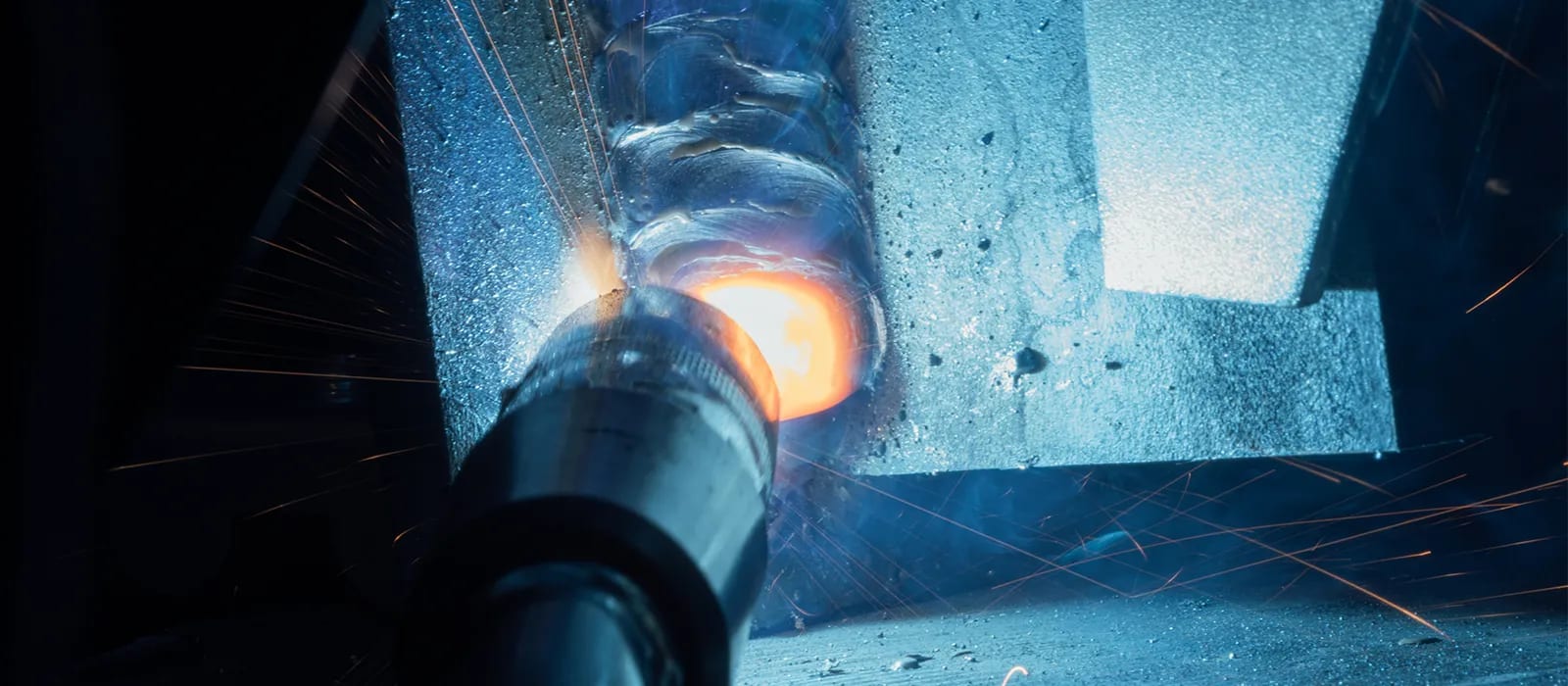
Advanced Solutions for Porosity Control
Executing sophisticated innovations and ingenious methods plays a critical duty in accomplishing superior control over porosity in welding procedures. One innovative remedy is check out here using sophisticated gas blends. Securing gases like helium or a blend of argon and hydrogen can help in reducing porosity by giving better arc stability and improved gas coverage. In addition, utilizing innovative welding techniques such as pulsed MIG welding or customized atmosphere welding can additionally assist reduce porosity problems.
One more sophisticated solution includes making use of advanced click to read more welding tools. As an example, utilizing devices with integrated functions like waveform control and innovative source of power can enhance weld high quality and reduce porosity risks. In addition, the execution of automated welding systems with exact control over criteria can substantially reduce porosity problems.
Moreover, including innovative monitoring and inspection innovations such as real-time X-ray imaging or automated ultrasonic testing can assist in detecting porosity early in the welding process, permitting immediate corrective actions. Generally, incorporating these innovative remedies can significantly improve porosity control and boost the total quality of bonded components.
Conclusion
In final thought, understanding the scientific research behind porosity in welding is important for welders and fabricators to produce top notch welds - What is Porosity. Advanced options for porosity control can additionally enhance the welding process and ensure a solid and reliable weld.
Report this page